Fall Protection Strategies for Refinery Shutdowns and Turnarounds
Posted by info@customdigitalsolutions.co BigCommerce on Oct 18th 2024
Fall Protection Strategies for Refinery Shutdowns and Turnarounds
Refinery shutdowns and turnarounds are essential maintenance periods in the oil and gas industry, but they also present significant fall hazards that require careful planning and protection. Understanding refinery fall protection and utilizing fall protection gear, such as safety harnesses, are crucial to mitigating these risks and ensuring worker safety.
Understanding Fall Hazards Specific to Refinery Operations
Refinery operations often require workers to perform tasks at heights, climb structures, and navigate complex layouts. Fall hazards are conditions that increase a worker’s risk of falling, for example, working on platforms, scaffolding, walkways, and tanks. The absence of proper guardrails, unprotected edges, and slippery surfaces due to spills or weather can increase the risk of falls. Providing proper fall protection equipment, such as leading edge self-retracting lifelines in the case of unfinished edge hazards, is a necessity in refinery operations.
Identifying Common Fall Risks During Shutdowns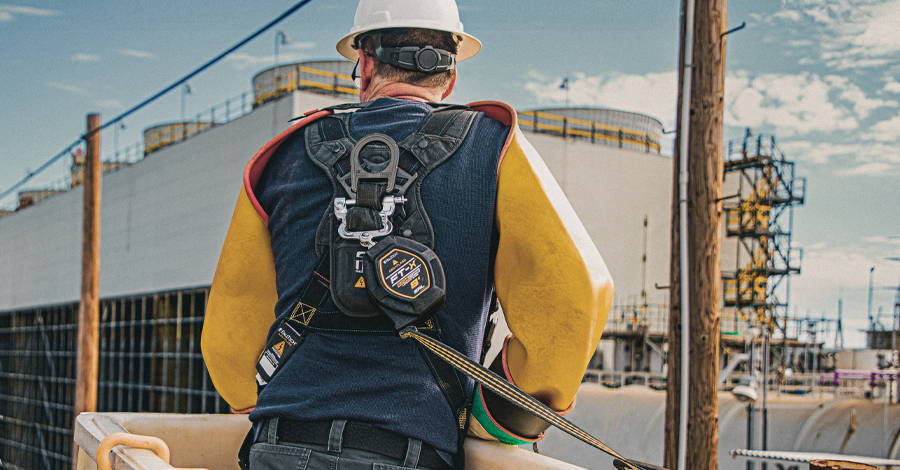
Shutdowns increase the risk of falls because they involve a lot of maintenance, inspections, and repairs. During shutdowns, scaffolds are built or taken down, and workers may need to enter tight spaces or climb to high equipment they don't usually use. The pressure to get these jobs done quickly, combined with the complexity of the tasks and the fact that many workers are new to the site, can increase the risk of falls due to temporary access solutions.
Impact of Refinery Layout and Work Height on Safety
Refineries are large, multi-level facilities with walkways, stairs, and platforms at different heights. The combination of vertical work, poor visibility, complex equipment, and narrow access paths creates a high risk of falls. Due to refineries’ massive size, it's difficult to continuously monitor potential hazards, making it essential to plan carefully to protect every area.
Evaluating Environmental Factors Affecting Fall Risks
Refineries can experience extreme temperatures, humidity, and exposure to chemicals, all of which can increase fall risks. Slick surfaces due to weather or process-related spills, strong winds, and limited lighting in certain areas can cause workers to lose balance or grip. Environmental factors also degrade safety equipment, which heightens risks if not regularly inspected and maintained.
Compliance with OSHA Standards for Fall Protection
The Occupational Safety and Health Administration (OSHA) regulates fall protection in the oil and gas industry under both its General Industry standards (29 CFR 1910) and Construction standards (29 CFR 1926). Whenever workers are exposed to a fall of 4 feet or more in general industry or 6 feet in construction, OSHA requires refinery fall protection be in place. The rules specify using guardrails, personal fall arrest systems (PFAS), and safety nets as needed.
Overview of OSHA Regulations Relevant to the Oil and Gas Industry
Specific regulations for fall protection in the oil and gas industry include OSHA's standards for walking-working surfaces (1910 Subpart D) and scaffold use (1926 Subpart L). The American National Standards Institute (ANSI) also provides guidelines for the performance of fall safety equipment, such as harnesses, lanyards, and anchor points, to ensure they meet strict safety standards (Z359 standards).
Ensuring Compliance During Refinery Maintenance Activities
Safety managers play a critical role in ensuring compliance during shutdowns. They conduct site-specific hazard assessments, coordinate with contractors, and enforce adherence to safety protocols. They also develop and implement fall protection plans, ensure equipment is available, and monitor work conditions to prevent protection lapses.
Implementing Comprehensive Fall Protection Solutions
Implementing a robust fall protection solution is crucial in refineries, where the high-risk environment puts workers in potentially dangerous situations. Falls from heights can have devastating consequences, including severe injuries or fatalities, financial losses, and operational delays. A comprehensive plan reduces liability, boosts worker morale, and ensures compliance with regulations. This includes mitigating risks when possible and using a fall protection hierarchy of controls.
Selection and Use of Personal Fall Arrest Systems
Safety professionals assess the job site and task requirements to choose the right PFAS. Typical required PFAS include a full-body safety harness, anchorage, and a connector like a lanyard or self-retracting lifeline. The type of equipment needed depends on the work height, available anchor points, and how much movement is required for the task. Getting a proper fit and regularly inspecting the equipment are mandatory steps in this process.
Installation of Engineered Fall Protection Measures
To prepare for maintenance, a refinery often builds fall protection into its design by installing permanent features like guardrails, ladder cages, and anchor points in key areas. During turnarounds, temporary solutions are added, such as scaffolding with built-in safety rails or portable fall arrest systems.
The Role of Fall Protection Specialists in Refinery Safety
Refinery fall protection specialists analyze refinery layouts to identify risks and recommend solutions, including the installation of fixed or temporary anchor points. They also train workers on the proper use of fall protection systems and inspect equipment to ensure it meets industry standards, making refineries safer in the process.
Conducting Pre-Shutdown Risk Assessments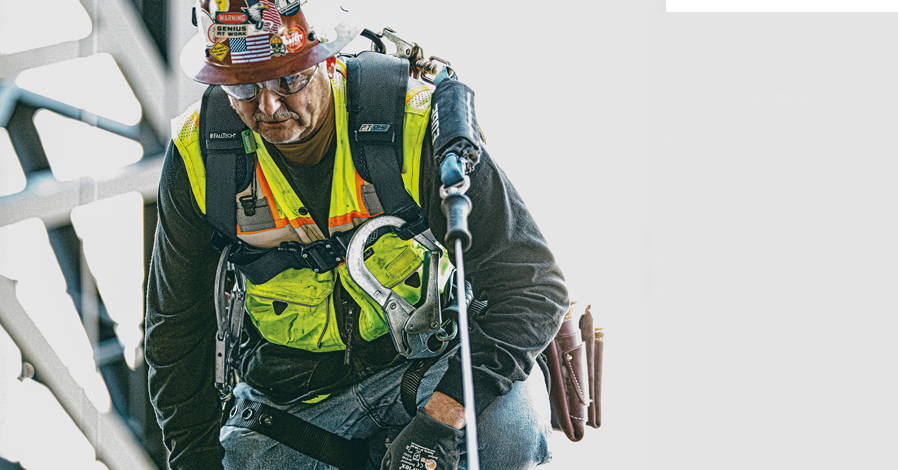
A pre-shutdown risk assessment identifies all potential hazards that workers may face during maintenance. A site walkthrough is conducted to evaluate elevated work areas, access points, and environmental conditions. This assessment helps inform the fall protection plan and tailor safety measures to the specific activities that will take place.
Tailoring Fall Protection Plans to Specific Site Needs
Refineries create fall protection plans that fit their individual layouts, heights, tasks, and environmental risks. A customized plan identifies specific hazards, selects the right equipment, and considers both permanent and temporary measures to cover every stage of work.
Training and Competency Development for Workforce Safety
Safety training teaches workers about the risks of working at heights and how to use fall protection systems correctly. Even with the best equipment, improper use can fail to provide adequate protection.
Essential Fall Protection Training for Refinery Workers
Workers should be trained to use personal fall arrest systems, inspect equipment properly, recognize fall hazards, and follow emergency rescue procedures. This training should be hands-on and led by a fall protection specialist so workers feel confident using the equipment in real-life situations. The training should also cover various product classifications, such as the difference between an ANSI Class 2 leading edge self-retracting lifeline and a Class 1.
Regular Refresher Courses and Safety Drills
OSHA standards may be abstract, but ANSI recommends refinery workers receive refresher training at least once a year, or more often if working conditions or equipment change. Regular fall safety drills, including rescue exercises, ensure workers and rescue teams are prepared for emergencies.
Enhancing Refinery Safety Through Strategic Fall Protection Planning
Strategic refinery fall protection planning is crucial for reducing risks during refinery shutdowns and maintenance activities. By identifying and addressing both permanent and temporary hazards, using the right equipment, and promoting a safety culture through training and compliance, refineries can greatly improve worker safety and operational efficiency during these critical periods.