The Role and Selection of Connectors in Fall Protection Systems
Posted by info@customdigitalsolutions.co BigCommerce on Feb 11th 2025
The Role and Selection of Connectors in Fall Protection Systems
Understanding Connectors in Fall Protection Systems
Fall protection connectors are the backbone of most fall protection systems, ensuring the system’s reliability and integrity. Understanding how to select and use these critical components will help create a safer environment for those working at height.
Definition and Role of Connectors
The US Occupational Health and Safety Administration (OSHA) defines a fall protection connector as “a device used to couple (connect) parts of the fall protection system together.” In other words, a connector links different parts of a fall safety system. Common connectors include snap hooks, lanyards, and self-retracting lifelines
How Connectors Enhance Worker Safety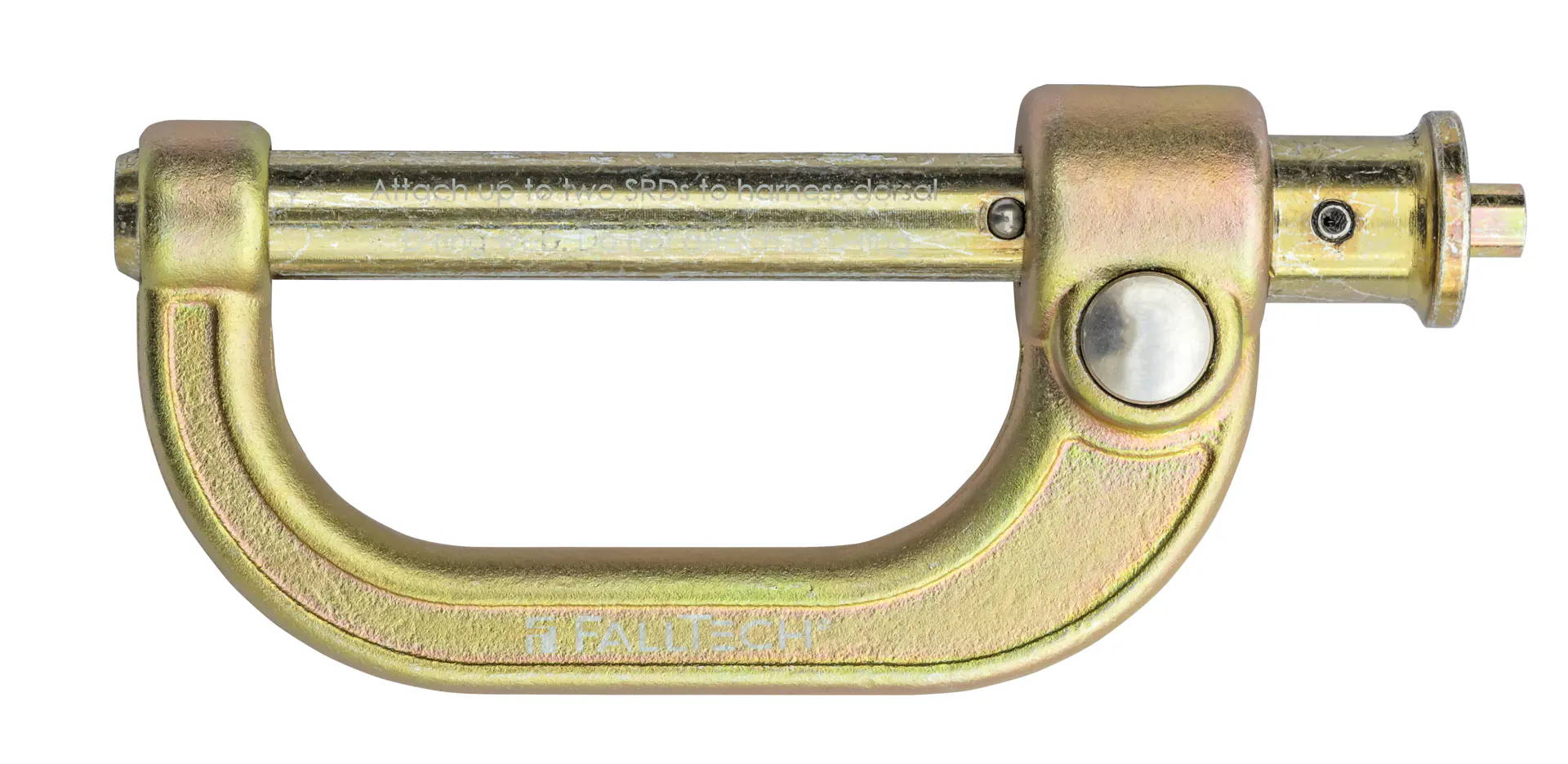
When you observe a worker utilizing a fall protection harness and lanyard secured to an anchor point via a connecting component, you’re seeing a “connected” system at play. All connectors must meet the highest safety standards because they are designed to stop a worker’s fall in progress. For instance, carabiners should be designed to prevent accidental disengagement by requiring two or more deliberate actions to attach or remove them from other components in the system.
Exploring Types of Connectors
Various types of connectors are designed to meet different worksite needs. Choosing the right connector is essential to enhance safety and efficiency on the job. Workers should be familiar with each connector’s specific functions and features to help them make the best choice when working at height.
Lanyards: Positioning vs. Shock-Absorbing
Positioning lanyards are intended to hold workers partially supported in their harnesses, enabling them to work hands-free to complete tasks. However, a positioning type of fall protection lanyard is not specifically designed to absorb the high arrest forces associated with a long free fall. In contrast, shock-absorbing lanyards are designed to dampen the force on a worker's body during a fall, reducing the risk of injury. However, they are not intended to support a worker leaning into the system to perform work duties.
Self-Retracting Lifelines (SRLs)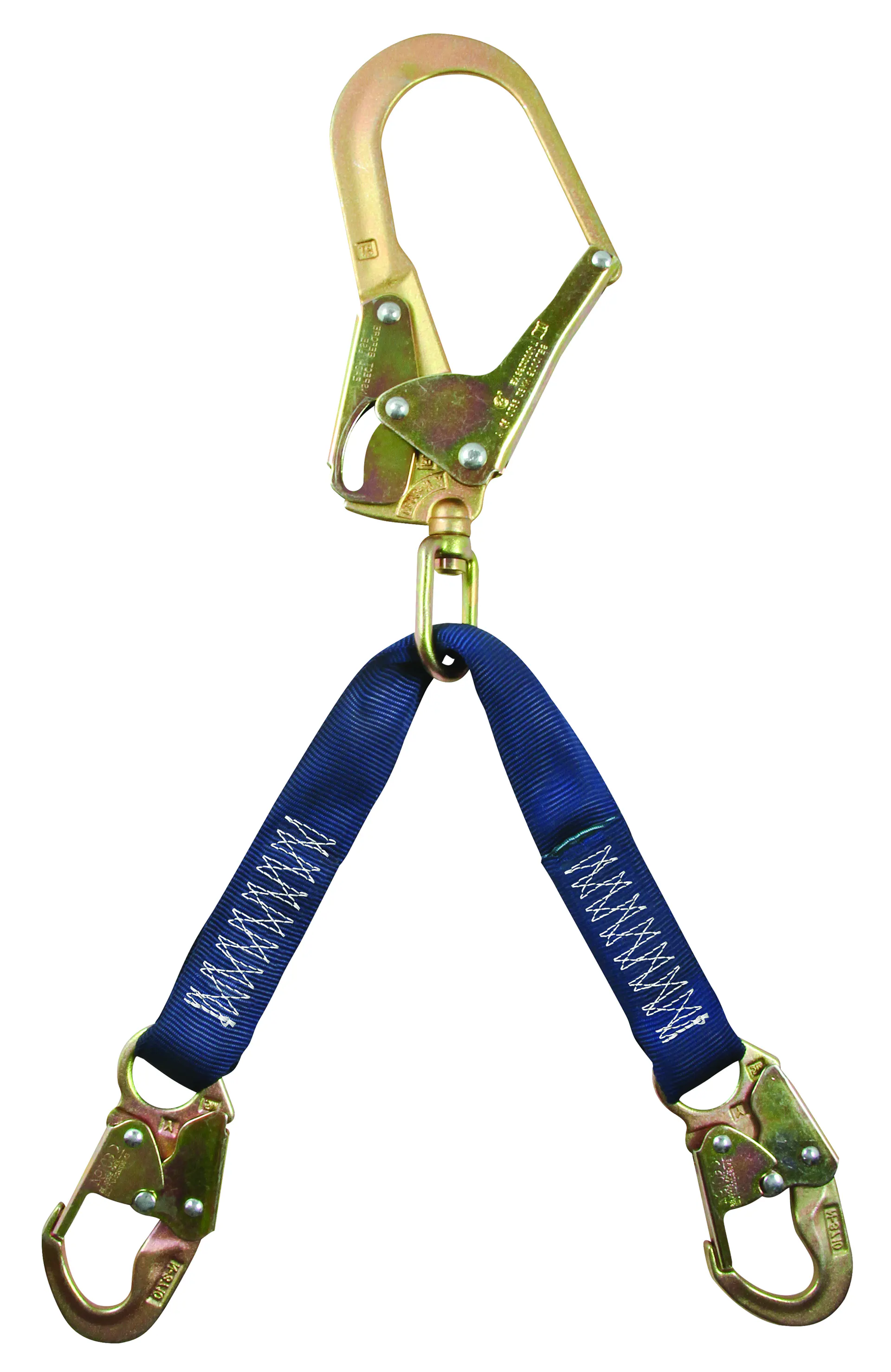
Perhaps the most popular type of retractable fall arrester, a self-retracting lifeline (SRL), is a fall protection device that adjusts its length as a worker moves. This evens out tension to reduce trip hazards. If a worker falls, the SRL locks to stop the fall, thus reducing the fall distance and impact force on the worker.
Many worksites have embraced SRL fall protection, making self-retracting devices the widely preferred fall protection connectors. The American National Standards Institute (ANSI) recently updated its standards and classifications for SRLs to better address their widening adoption. SRLs fall into standard SRL, personal SRL-P, and rescue/retrieval SRL-R types.
These types are further divided into Class 1 or 2 categories. A Class 1 SRL is designed to anchor at or above a worker harness’s dorsal D-ring. A Class 2 SRL is designed to anchor at, above, or up to five feet below a worker’s dorsal D-ring. Additionally, a Class 2 SRL has a lifeline designed for use in proximity to leading edges.
Vertical Lifeline Systems and Their Components
A vertical lifeline (VLL) system is designed to protect workers as they move up and down structures or ladders on a vertical or sloped plane. These systems consist of a specialized rope that serves as the vertical lifeline and additional components such as fall arresters (commonly known as vertical rope grabs), a lanyard, and a counterweight.
Anchorages and Anchorage Connectors
Anchorage is the base structure of a user’s fall protection system. An anchorage connector is the device or component that connects the user’s fall protection system to that base structure.
Criteria for Selecting the Right Connector
Choosing the right connector is crucial for worker safety and can enhance efficiency when working at height. The connector must be appropriate for the worksite conditions, provide the necessary mobility, and be suitable for the specific task. Proper selection and use help maintain a secure attachment between an anchorage connector and the anchorage itself, reducing the risk associated with falling.
Assessing Work Environment Suitability 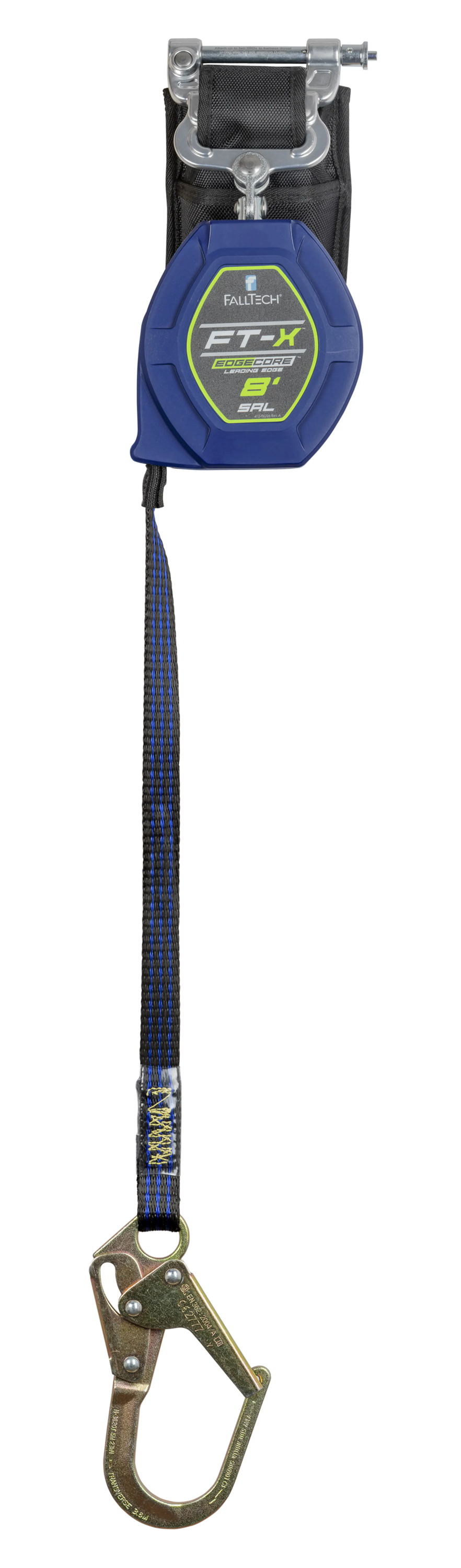
Selecting the appropriate connector for a worksite involves thoroughly assessing potential hazards. A safety manager must consider the mobility requirements and ensure compatibility with other safety gear. Other factors must also be evaluated, such as exposure to corrosive substances, temperature extremes, and the need for quick or frequent connection changes. Considering these elements ensures the chosen connector is effective and safe for the specific environment.
Mobility Requirements and Connector Types
When selecting a fall protection connector, it's important to consider the mobility requirements of the worker performing duties at height. The connector should be long enough to allow the worker to complete their tasks but not so long that it creates excessive fall distances and forces on the system in the event of a fall. For example, a worker who remains relatively stationary may benefit from a four-foot shock-absorbing lanyard, offering safety without adding excess length to the system. Conversely, a worker needing greater mobility should consider a lengthy retractable lifeline, which provides extended movement while minimizing excessive slack in the system.
Evaluating Fall Clearance Needs
Fall clearance calculations are vital to correctly applying a fall protection system. These calculations determine the total potential fall distance for a specific system, establishing the distance needed to arrest a worker's fall and prevent contact with structures or surfaces below their work-at-height location. Select connectors based on the available clearance. Users can find fall clearance charts within the shock-pack of their ANSI Class 2-rated self-retracting lifelines.
Ensuring Connector Compatibility and Compliance
Connector compliance and compatibility are crucial for safeguarding systems and workers. They help ensure seamless interaction between components, even under duress. This practice mitigates potential hazards and fosters a robust, reliable operation.
Compatibility with Other Safety Components
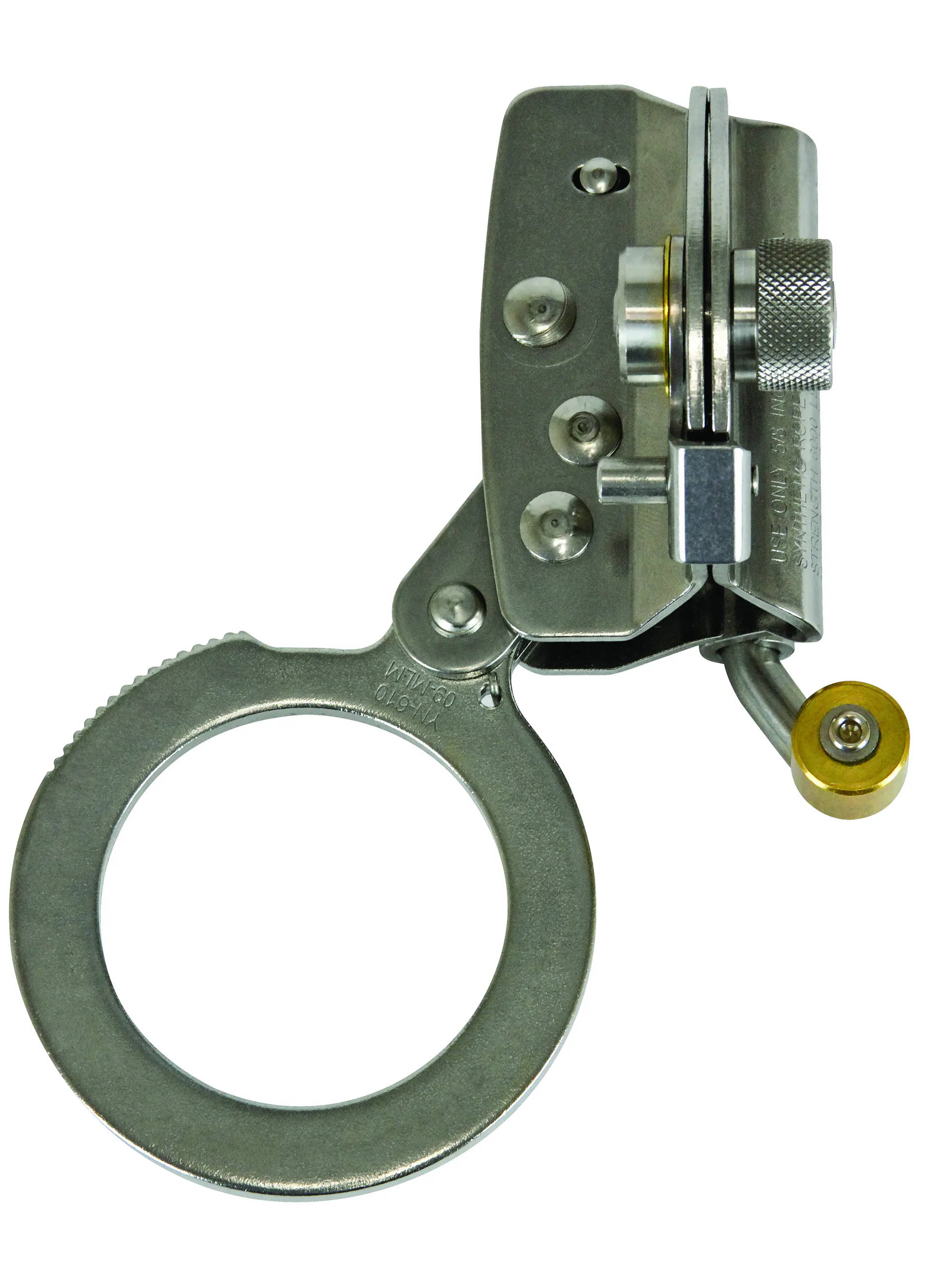
A cohesive fall protection system safeguards workers and prevents equipment failures. A mismatched connector within that system compromises its integrity, undermining safety and increasing the risk of accidents. Vigilance in selecting compatible gear creates a strong defense against falls. Every connection counts in a well-designed fall protection strategy. Always check with the connector’s manufacturer to verify compatibility or purchase an industry-specific fall protection kit to ensure all included components are compatible.
Adherence to Industry Standards and Regulations
Though OSHA offers little guidance regarding fall protection connectors, the ANSI/ASSP Z359 Fall Protection Code provides comprehensive testing and performance standards. Rigorous testing and certification ensure these vital components perform reliably under extreme conditions. Compliant connectors reduce equipment failures and workplace accidents. Adhering to safety regulations and using equipment that meets industry standards provides workers with a higher level of protection.
Remember: Tough standards save lives.
Key Features of High-Quality Connectors
Reliable fall protection hinges on robust connectors. These vital components must be capable of absorbing high-impact loads and enduring wear, safeguarding users from harm. By withstanding dynamic forces, connectors ensure consistent performance over time. Strong, energy-dampening connectors, such as shock-absorbing lanyards, are key components of any effective fall arrest system.
Safety Features: Self-Closing and Locking Mechanisms
Secure connections in fall protection rely on self-closing and locking mechanisms. These features work in tandem to prevent accidental disengagement. Some vertical rope grabs, for example, feature double-locking closures that prevent accidental openings. Self-closing gates snap shut automatically, while locking systems require intentional unlocking. This dual approach ensures connectors remain firmly attached, enhancing users’ safety. The combined mechanisms create a robust safeguard against potential hazards during equipment use.
Usability and Durability Considerations
Workers must trust fall protection connectors and be able to use them easily. Straightforward operation in diverse settings minimizes errors, and robust construction provides sturdy, reliable connectors. The design should be user-friendly and use long-lasting materials such as aluminum or steel. Such connectors prove indispensable, offering steadfast protection when lives hang in the balance.
Importance of Shock Absorption in Connectors
When a worker falls, a shock absorber, such as those found in most modern self-retracting lifelines, springs into action. The shock absorber dissipates energy, softening the fall's impact. This safer, gentler arrest minimizes injury risk and maximizes worker safety
The Importance of Training and Regular Inspection
Training and regular inspections are vital when using any fall protection equipment. Understanding proper usage and detecting potential damage or defects helps ensure workers at height can use their equipment confidently.
Training Workers on Proper Connector Usage
Selection and application of fall protection connectors require a solid understanding of fall safety principles. Workers must receive proper fall protection training before working at height and using this equipment. Workers using shock-absorbing lanyards, for instance, should know how to identify their minimal fall clearance. This training helps prevent misuse and enhances overall worksite safety. With this knowledge, fall protection systems perform as designed, preventing accidents and injuries.
Search for a fall safety course in your area. Fall protection equipment manufacturers may offer instructional courses by region.
Routine Inspection Protocols for Connectors
Inspect connectors for cracks, corrosion, deformities, or any other potential issues that may affect proper functioning. Test gates and locks to ensure smooth operation. Verify all markings and certifications. Identify any damage that compromises safety, such as a bent anchorage connector or twisted O-rings on vertical rope grabs. Follow the manufacturer's inspection schedules and standards. Regular checks guarantee continued safety and reliability. Vigilant maintenance prevents accidents and extends the equipment's lifespan. Properly functioning connectors are essential for user protection and operational efficiency.